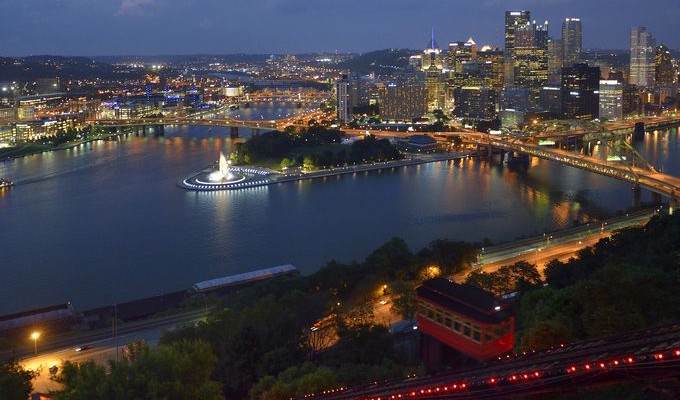
Septic dye test
A dye test is a relatively low cost, non-invasive method for testing of private sewage treatment systems. It is a limited, performance based test. This test does not provide a guarantee of the present, or future, performance of the system. It is not a full evaluation of a sewage treatment system, but nonetheless provides valuable information regarding the present performance of the system. A septic dye test is ideally suited for evaluation of septic systems for real estate sales purposes, since the test does not result in damage to the property, as would any excavation, and provides minimal disruption of the occupant's use of the home during the test. More comprehensive testing and evaluations are possible, and may be desirable, if greater assurance is needed.
Property & System information
If the septic tank has been pumped within the past 30 days, the inspector will need to determine that the tank is filled prior to conducting the dye test or postpone the test. Any alteration of the system within the previous 30 days constitutes a valid reason to postpone the dye test. The client is encouraged to contact the contractor performing the work to determine the nature and purpose of any alterations or pumping, the physical condition of the tank at the time it was pumped, reason for pumping, and frequency of pumping.
The client should be encourage to review any documentation regarding the system(s) to determine that the system was approved by the appropriate authorities when installed or modified.
A review of any records by the inspector is not required, but may, if readily available, be helpful in determining the system age and location of components.
Owner interview, if feasible
Interview the owner of the property regarding the system history and record the information.
Waste Treatment system inspection Assessments include:
1. inspection of visible interior plumbing to determine the likely number of treatment systems,
2. visual inspection of exposed components of the sewage treatment system,
3. dye testing, and
4. written report.
Interior Plumbing
Visually check all plumbing discharges for the house; running water from various fixtures to hear and verify discharge.
Look for the discharge of storm water (footing drains, sump pump, downspouts, etc.) to the sewage treatment system
Visually check in the basement for evidence of sewage backup. Flush lowest level toilet to check siphon for evidence of backup.
Sewage Treatment system
Attempt to visually confirm the location of the septic tank, distribution box and absorption area. Excavation, probing, or snaking are not required. Observe any readily accessible components.
Look for evidence of potential problems (odors, seepage of sewage, saturated soil, lush vegetation, etc.
Visually check the area for adequate surface drainage.
Visually check areas adjacent to the absorption area for evidence of failure or breakout.
Visually check for pumps or dosing systems. Note if there is an alarm system. Visually check for evidence of overflows. Observe the pump operation. For holding tank systems, observe the level if practicable.
Observe any drainage pipes on the property that may affect or be affected by the treatment system(s). Observe any evidence of sewage system discharge from the drainage pipes.
Dye testing
Inform the owner (if available) of the volume of water and rate of flow required for the dye test.
The required volume depends on the number of bedrooms, use of reduced flow plumbing fixtures, and the existence of any whirlpool tubs. The intention is to approach short-term system capabilities while avoiding inordinate use of the water supply. The desired flow rate and volume for the dye test are as follows:
Flow rate should not be less than 3 gpm nor should it exceed 5 gpm.
The volume should be 50 - 75 gallons per bedroom (plus a maximum of 50 gallons for each whirlpool tub), with 100 gallons minimum.
For holding tanks the volume need only be sufficient to determine that all discharges enter the tank.
If the property has separate (multiple) discharges, split the required volume proportionally between the systems being tested roughly equivalent to normal use patterns.
Introduce dye into the system through one or more fixtures. If there is doubt concerning the connection of fixture(s) or a separate dwelling to the system, the use of separate color dyes for these fixtures may be helpful.
Introduce a fluorescent dye immediately prior to running the required amount of water. The dye manufacturer’s instructions should be followed.
Run water from as many fixtures as necessary to maintain the required flow rate. Use best professional judgment.
Visually inspect the absorption area and adjacent ditches, watercourses, etc. for evidence of dye or sewage effluent.
Visually check for any alternate sources of effluent such as an adjacent property.
Visually check for evidence of effluent entry into the basement.
Flush lowest level toilet to check siphon for evidence of system backup.
Written report of dye test result.
A written report of the dye test should be provided to the client.
The report should document the nature of the dye testing including: flow rate, time of flow, total volume of water, and point of introduction of dye and water.
The report should describe/identify, as applicable, the:
- preceding and current weather conditions;
- type of water supply and water conditioning equipment;
- number and type of private waste treatment systems observed;
- components of the private waste treatment system observed (the existence of covered components cannot be confirmed unless access points are exposed);
- any vegetation, grading, drainage, driveways, patios, walkways, and retaining walls that appear to impact the waste treatment system; and
- suitability of access to any components.
The report should document any conditions indicating failure and the location of any failure. Any of the following conditions establish that the system(s), including any "gray water" systems, have failed the dye test:
1. evidence of breakout of effluent, backup of effluent, or surfacing of dye; or
2. evidence of wastewater discharge to a watercourse.
The report should include the results of the owner interview, if applicable.
The report should include any exclusions or limitations to the testing.
The report may also include maintenance recommendations and any visual evidence of missing, unsafe, or deteriorating components
Notes:
Limitations of Dye Test A dye test can not identify all types of wastewater treatment system failures. By itself a dye test is not indicative of the overall condition of the system. Snow, ice, vegetation, and leaf cover can hide surfacing effluent. Because the components of the system are buried, no guarantee can be made regarding the location or condition of private sewage treatment system components unless specific additional tests such as opening the septic tank, pumping the septic tank, and excavation are ordered. These tests are not part of a Sewage Treatment System Dye Test.
Scheduling Sellers/buyers may need to plan on conducting testing prior to listing or after closing; dye tests are more reliable for an occupied property and snow cover may obscure some visual clues.
Pumping of Septic Tank Only by pumping and visual inspection can actual septic tank capacity and condition be completely determined. Probing in the area of a tank is not recommended; the probe may damage fiberglass and steel tanks. Steel tanks last 20-25 years, rust, and collapse. Since steel tank tops may be replaced while leaving the old tank in place, the condition of the top is not a reliable indication of tank age/condition. Concrete and fiberglass tanks may crack; baffles may be damaged allowing solids into the absorption field. When property ownership is changing, it is highly recommended that the septic tank be pumped and visually inspected after the dye testing but prior to closing.